Stiffened panel buckling¶
Introduction¶
The following figure presents a stiffed panel subject to buckling on a military aircraft.
This use-case implements a simplified model of buckling for a stiffened panel (see [ko1994]).
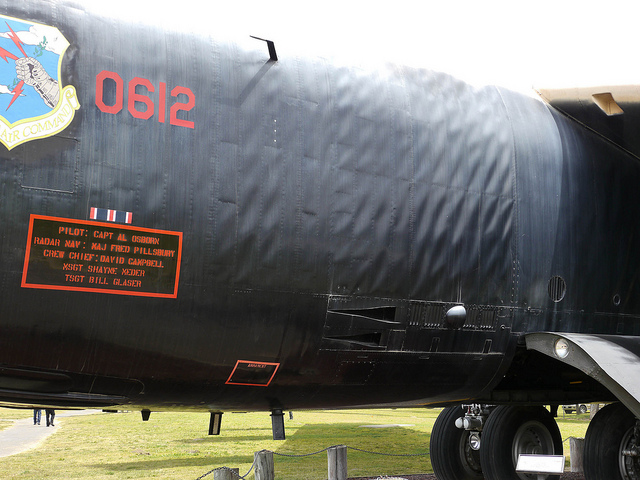
Figure 1. Buckling of a stiffened panel.¶
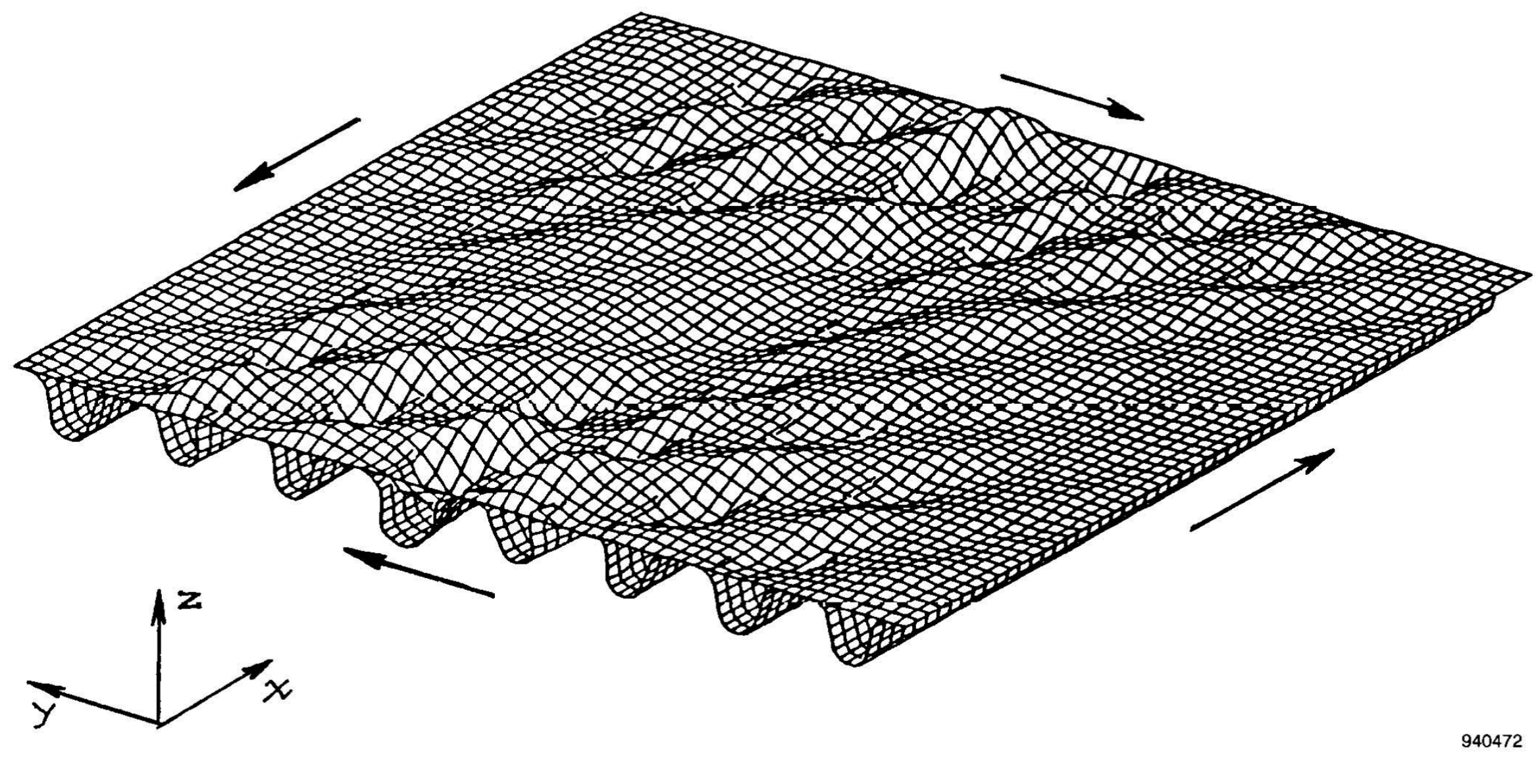
Figure 2. 3D simulation of buckling.¶
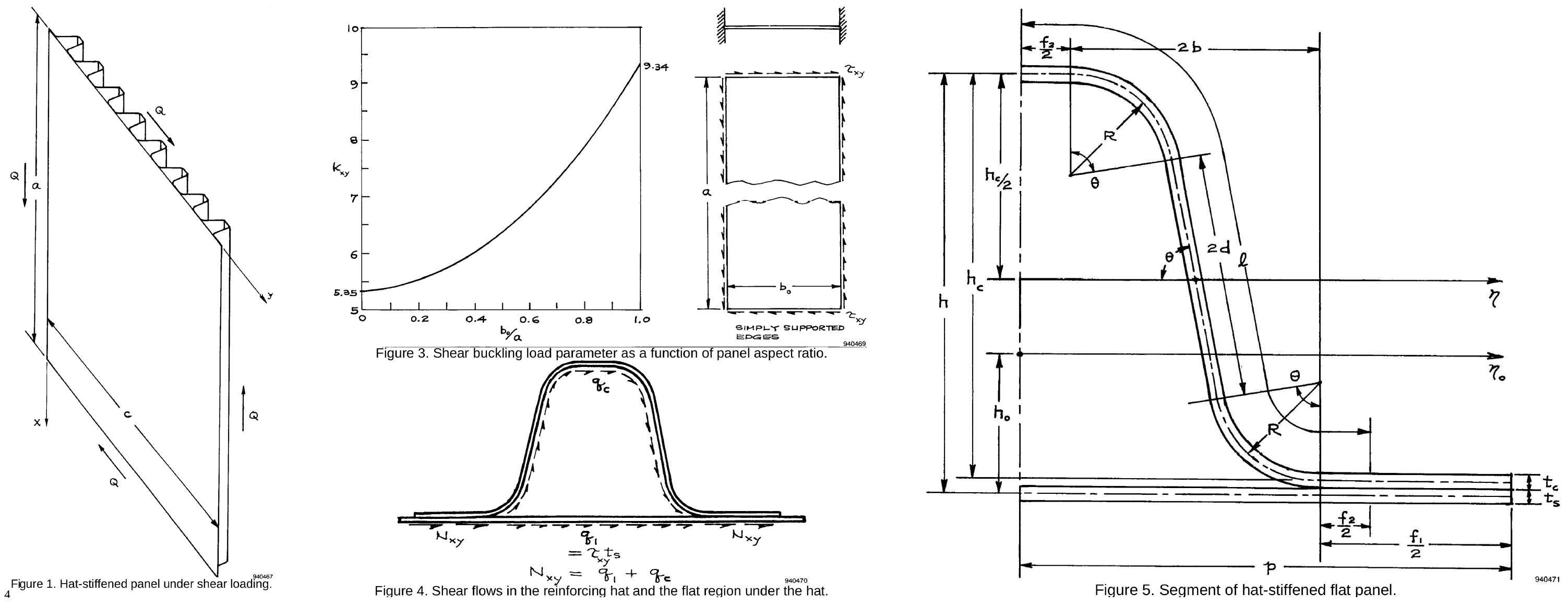
Figure 3. Parameterization of the stiffened panel.¶
This test case is composed of nine random variables:
: Young modulus (
)
: Poisson coefficient (-)
: Distance between the mean surface of the hat and the foot of the Stiffener (
)
: Length of the stiffener side (
)
: Width of the stiffener foot (
)
: Width of the stiffener hat (
)
: Thickness of the panel and the stiffener (
)
: Width of the panel (
)
: Distance between two stiffeners (
)
: Half-width of the stiffener (
)
The output of interest is:
: the critical shear force (
)
We assume that the input variables are independent except the and
for which we measure a Spearman correlation of
,
modelled using a
NormalCopula
.
The critical load of a stiffened panel subject to shear load is:
where:
is the width of the panel;
is the width between too consecutive stiffener feet;
is the thickness of the panel main surface;
is the Young modulus of the panel main surface;
is the Poisson coefficient of the panel main surface;
is the bending coefficient of the panel main surface:
is the load factor associated to shear buckling. It is given as a function of
through the empirical equation:
It is more convenient to use the shear force instead of the shear
stress component
. It leads to the equation:
where abd
are the shear fluxes in the panel main surface
and its stiffener. They are given by:
and:
where:
is the shear modulus of the panel main surface:
is the torsion strain of the panel main surface;
is the shear coefficient of the stiffener:
is the thickness of the stiffener;
is the distance between the mean surfaces of the stiffener hat and foot;
is the distance between the mean surfaces of the stiffener hat and the panel main surface:
is the width of the foot of the stiffener;
is the width of the hat of the stiffener;
is the half-widht of the stiffener;
is the radius of the circular part of the stiffener;
is the angle of the circular part of the stiffener;
is the length of the stiffener flank;
is the half-lenght of the straight part of the side of the stiffener;
is the area of the section of an half-ondulation;
is the area of the section of the full panel (main surface and stiffener) bounded by
:
is the distance between the mean surface of the panel main surface and the global geometric center of the panel:
It leads to:
and finally, is given by:
For industrial constraints, the stiffener and the main surface are cut in the
same metal sheet, so ,
,
.
The final expression of the critical shear force is then:
with:
;
;
;
.
References¶
Load the use case¶
We can load this model from the use cases module as follows :
>>> from openturns.usecases import stiffened_panel
>>> sp = stiffened_panel.StiffenedPanel()
>>> # Load the stiffened panel use case
>>> model = sp.model()
API documentation¶
- class StiffenedPanel
Data class for the stiffened panel model.
Examples
>>> from openturns.usecases import stiffened_panel >>> # Load the stiffened panel model >>> panel = stiffened_panel.StiffenedPanel() >>> print("Inputs:", panel.model.getInputDescription()) Inputs: [F,L,a,De,di,E] >>> print("Outputs:", panel.model.getOutputDescription()) [Deflection,Left angle,Right angle]
- Attributes:
- dimConstant, the dimension of the problem.
dim=10
- model
SymbolicFunction
Model of the critical shearing load. The model has input dimension 10 and output dimension 1. More precisely, we have
and
.
- EYoung modulus (Pa),
TruncatedNormal
distribution ot.TruncatedNormal(110.0e9, 55.0e9, 99.0e9, 121.0e9)
- nuPoisson coefficient (-),
Uniform
distribution ot.Uniform(0.3675, 0.3825)
- h_cDistance between the mean surface of the hat and the foot of the Stiffener (m),
Uniform
distribution ot.Uniform(0.0285, 0.0315)
- ellLength of the stiffener flank (m),
Uniform
distribution ot.Uniform(0.04655, 0.05145)
- f_1Width of the stiffener foot (m),
Uniform
distribution ot.Uniform(0.0266, 0.0294)
- f_2Width of the stiffener hat (m),
Uniform
distribution ot.Uniform(0.00627, 0.00693)
- tThickness of the panel and the stiffener (m),
Uniform
distribution ot.Uniform(8.02e-5, 8.181e-5)
- aWidth of the panel (m),
Uniform
distribution ot.Uniform(0.6039, 0.6161)
- b_0Distance between two stiffeners (m),
Uniform
distribution ot.Uniform(0.04455, 0.04545)
- pHalf-width of the stiffener (m),
Uniform
distribution ot.Uniform(0.03762, 0.03838)
- distribution
JointDistribution
The joint distribution of the input parameters.